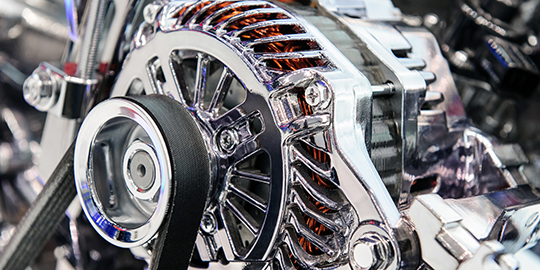
'Auto component makers must focus on quality to reduce imports'
The automobile industry has asked their component suppliers to focus on developing technology-based high-end products through improvisation and innovation in order to match global quality standards and reduce imports. “What the industry has achieved in last 10 years is commendable. 3x (three times) growth in revenue, 5x (five times) growth in export, but at the same time export is lower than the import. That means approximately Rs.80,000 crore sitting there, which could come on this side of ‘Make in India’ when you import it,” said Pawan Goenka, Executive Director & Group President (Automotive & Farm Sector), Mahindra & Mahindra. “We still lack technology to develop high-end components,” Goenka said citing an example of air bags that are mostly imported in India. His remark came at a time when Indian automotive industry is looking to manufacture all components within the country to minimise imports taking advantage of the “Make in India” initiative launched by the government. Though India’s automobile export increased to $11.2 billion during 2014-15, the annual import in this sector remained significantly higher, at $14 billion, registering an increase of 7.5% compared to the same period a year ago. Suzuki Motor Corporation Chairman Osamu Suzuki also urged the Indian auto component manufacturers to embrace “Quality in India” to ensure the growth of the industry. “I would like to add ‘Quality in India’ to ‘Make in India’. I believe in case all suppliers follow the ‘quality of India’ then they will overcome America and China, and they can acquire No. 1 position in the global market,” he said at a conference of Automotive Component Manufacturers Association of India (ACMA) held in New Delhi. India’s automobile industry has been facing several quality scrutinies amid frequent incidents of vehicle recalls owing to their faulty parts. “The news of recall of more than 1 million units is fluttering in global market, hence it doesn’t leave any room for doubt that quality is an important key. I request all of you to reinvest your profit which you are earning from component manufacturing in the same business,” he added. In August 2015, General Motors India recalled 1.5 Lakh units over battery issue, and Harley Davidson recalled its Street 750 Cruiser bikes over faulty fuel pump. In June-July this year, Nissan India recalled 12 thousand units to fix problems with their airbags and engine switch. Since July 2012, more than 10 Lakh units have been recalled in India, including that of top car makers Audi India and Jaguar Land Rover. Among the country’s top car manufacturers, only Tata Motors and Volkswagen haven’t recalled any vehicle for over three years. July 2013-June 2014 marked the worst year for India’s car manufacturers when they recalled more than 5.2 lakh units. Analysts say that the ratio of defective components in India-made vehicles is higher than the global average. “Approximately five-six years ago, our consultants said the world’s best companies have 0.2% defect per vehicle. Average defect in Japan and Europe stood at somewhere 0.4%. Initially hesitant to reply, when asked about where we stood, he (the consultants) finally told us that you were at 7.8% defect per vehicle,” said Vinod K Dasari, Vice President of Ashok Leyland, a leading brand in commercial vehicle segment. “We called our suppliers together and launched a massive initiative to rectify that. And today I am proud to say that over the last couple of years we have been consistently below 0.3%,” Dasari added.
September 05, 2015 | 3:32pm IST.